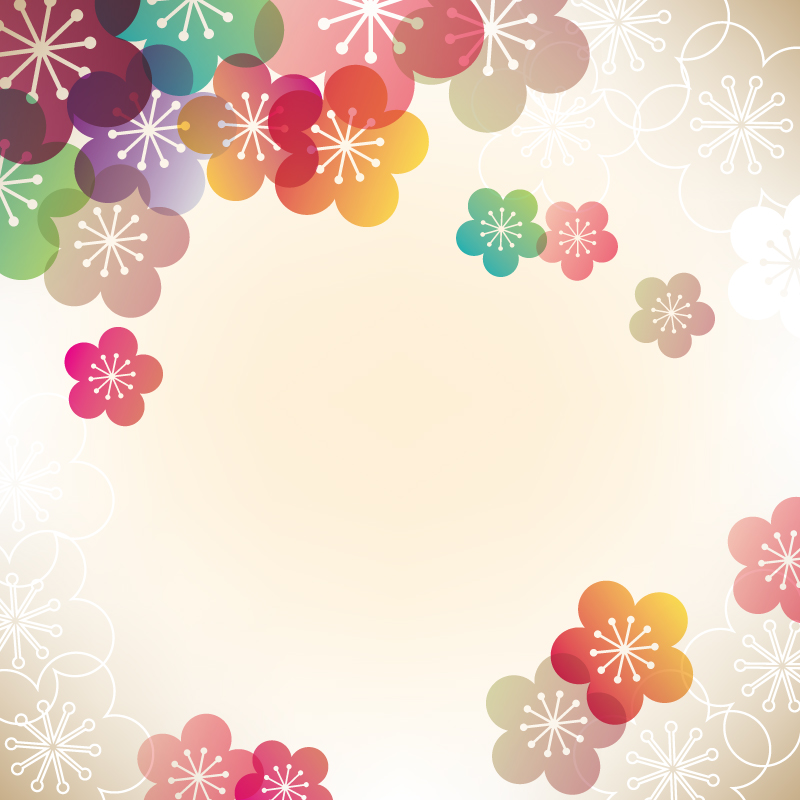
Sharon Severn gives us her insights on the Six Sigma process
Six Sigma efforts target three main areas:
• Improving customer satisfaction
• Reducing lead time
• Reducing defects
The world of improvements does not need to be as complicated as the above points sound. One of my personal phrases is “if it irritates me, then do something about it – improve it”. By using this simple instinct, I have improved so many processes during my working career. I attained my Six Sigma Green Belt “Creating Excellence” by improving secretarial processes and behaviours, of which I am very proud.
My first article will be an insight into 5S. In the next Executive Secretary Magazine issue, I will reveal how I attained my Green Belt in Six Sigma from a PA’s point of view.
One of the most copied systems to come out of Japan is known as “the five Ss”. At first glance, it seems rather simple. After all, it is just about being tidy. So why have so many companies implemented it?
Less is definitely more.
The simplicity of the five Ss is actually its key strength. Too many companies seek to implement more complex systems, possibly to justify the consultant’s fee and possibly to excuse their past negligence. People can struggle not only with the change, but also making sense of the new approaches. A critical value of simple systems is that they are relatively easy to understand and implement. Of course the change management aspects of any new approach can be complex and difficult, and implementing the five Ss can have its difficulties, but this is at least minimised by the basic nature of the system.
The five Ss are described briefly below, both in Japanese and the English translation.
JAPANESE – ENGLISH
Seiri – Sort
Determine what is required and what is not, in the amount needed and only when needed.
Seiton – Straighten
Arrange items that are needed so that they are easy to use, labelled and anyone can find them and put them away.
Seiso – Sweep
Clean and sweep on a regular and frequent basis, so that when you need something, it’s there and it works.
Seiketsu – Standardise
Revisit the first three of the five Ss on a regular and frequent basis and consolidate with standard procedures.
Shitsuke – Self-Discipline
Sustain and improve five S activities through policy.
Implementing the five Ss requires the full cooperation of all involved, and is an amazingly powerful activity.
When people realise that these simple activities have such power and that by implementing them, the workplace becomes a more pleasant place, the principles will undoubtedly be acted on with enthusiasm.
The five Ss originated in a manufacturing environment, but work extremely well in other work situations – for managers, shop-floor workers and even at home.
How do I implement this into my environment?
•Take a “before” photograph of the identified (untidy) area.
•Audit the area with a score 0-5 (0 being very poor).
•Sort and throw away what is not required. Red tag what is of value (personal items and people not included!).
•Straighten and sweep
•Red tag items go for “auction”. If not wanted – bin them.
•Take an “after” photograph.
•Audit regularly (monthly).
To summaries five S guidelines:
•No-one is to blame for how things are today.
•Five Ss are the responsibility of everyone
•Use the power of the team – everyone is an expert.
•Five Ss are an attitude of mind as well as a practical tool.
•Five Ss are continuous, don’t rely on one-day events.
•Always address safety issues immediately.
•Use your head not your wallet
•Think of how to make it work, not why it won’t.
•Establish the start point – things can only get better!
•Use audit sheets to assess each area.
•Take pictures of the before condition and make reference to where they are for future comparison.
•Record other problem areas, such as safety issues or machine breakdown.
I hope you have enjoyed reading this article and look forward to writing my next article.
Thanks for talking about An Introduction to Six Sigma – Loved it!
Hello Sharon,
My colleagues and myself are currently in a Green Belt Project with the focus on Administrative Assistant Efficiencies then and now (since the pandemic). Our goal is to prove that the “work arounds” and electronic/digital environment that we have been forced to create will provide for a more efficient and cost saving work place when we actually do return to the office. I have enjoyed your articles and would to see your story board if it is published somewhere. Thank you very much and wish me luck!
Teresa McKenzie